3,175 Industrial Management jobs in India
Supply Chain
Posted today
Job Viewed
Job Description
- Sr Program Manager: Supply Chain Planning and Logistics- Exposure to Project Management methods
- Good communication and presentation skills
- Manpower planning, development, allocation and deployment
- Keep the employee commitment level high and increase retention
- Safeguard the critical resources and information
- English, German or International Experience/Strong Interest
- Developing Business in own area of responsibility in alignment with MBRDI vision
- Operational excellence
- People and process management
- Effective engagement with the customers and Suppliers
- Building and managing teams
- Ensure Knowledge build-up of team members, performance monitoring and feedback
Required skills:
- Developing Strategy and Business in alignment with customers
- Supply chain Planning -Inbound, Outbound &Transportation logistics for MB Plants and Warehouses
- Enable on time delivery and quality of projects along with value additions. Identify new areas to vertically and horizontally expand scope of work
- Develop innovation and digital avenues and platforms for SC. Provide new ideas and technologies to create digital hub in India
- Design inbound planning - Supplier selection, TLC, delivery methods, Design for logistics- Lead the projects and coordinate with stakeholders
- Provide technical support on designing the inbound logistics
- Development of innovative strategies to digitalize the planning process
Design outbound logistics- Outbound logistics transportation planning and optimization
- Milk run, route optimization, EC, costing and service provider selection
- Setting up control center and offshore operations
**Qualifikationen**:
Supply Chain
Posted today
Job Viewed
Job Description
**Job Types**: फ़ुल-टाइम, पार्ट-टाइम, नियमित / स्थायी, फ्रेशर, फ़्रीलांस
Contract length: 12 months
Part-time hours: 20 per week
**Salary**: ₹५०,०००.०० per month
**Benefits**:
- बदला जा सकने वाला शेड्यूल
Ability to Commute/Relocate:
- Mumbai, Maharashtra: Reliably commute or willing to relocate with an employer-provided relocation package (preferred)
**Experience**:
- total work: 1 year (preferred)
**Speak with the employer**
+91
Supply Chain (Supply Planning)
Posted today
Job Viewed
Job Description
**Supply Chain (Supply Planning)**
**About **GlobalFoundries**
**Essential Responsibilities include**:
- Process demand commits, customer order, and customer demand forecasts in ERP/APS and internal forecast tool.
- Cross functional Collaboration on forecast deltas based on actual customer demand.
- Build weekly Master Production Plan based on consensus demand plan using APS.
- Ensuring availability of raw materials by providing appropriate data to Material Planning team.
- Gather and review timely supply status with Fab execution team to ensure undisrupted supply continuity.
- Analyze WIP data to determine supply status and work through constraints or challenges to on time delivery.
- Develop and implement capacity plans to meet demand in co-ordination with Industrial Engineering team. Identify long range throughput constraints & align engineering efforts and manufacturing strategy accordingly.
- Collaborate internally with respective teams on backlog reviews or customers’ requests on order schedule changes and ensure that delivery schedules are met in a timely manner and communicated to customers and internal sales department.
- Inventory flow control by making sure customer demand is met on time.
- Collaborate with Logistics and OSATs for timely shipments of materials to meet the customer schedules.
- Analyze and resolve transactional/system issues to avoid any delays in shipment schedules.
- Work with cross functional groups (example: Yield Engineering, Customer Engineering, Turnkey Operations, OSAT Operations, Modules, Manufacturing, Sales) on production and qualification issues.
**Other Responsibilities**:
- Perform all activities in a safe and responsible manner and support all Environmental, Health, Safety & Security requirements, and programs
**Required Qualifications**:
- Education - Bachelor’s Degree in Engineering/Masters.
- Experience - bachelor's degree with 6-8 years, master's degree with 5-7 years of relevant experience in Supply chain, manufacturing, production planning, demand management, and/or business consulting
- Excellent communication, presentation, facilitation, time management, and customer relationship skills and should possess professional behavior.
- Should be well versed with Supply chain finance & revenue management
- Should have a good understanding of Supply chain planning & scheduling, Inventory management, Demand planning and forecasting
- Should have excellent analytical capabilities and presentation skills
- Should have excellent excel, advanced excel and Power BI, SQL, skills
- Basic knowledge on data extraction from database like Oracle/SAP/others.
- Should have progressive mindset towards business and responsibilities.
- Travel - (15% of travel required)
- Language Fluency - English
**Preferred Qualifications**:
- Experience with planning systems like i2 JDA/Kinaxis RR/O9 solutions/SAP IBP.etc
- Practiced in ERP systems (Oracle or SAP)
- Knowledge of Supply Chain Management and core principles (APICS Cert. or equivalent a plus)
Supply Chain (Supply Planning)
Posted today
Job Viewed
Job Description
**Supply Chain (Supply Planning)**
**About **GlobalFoundries**
**Essential Responsibilities include**:
- Process demand commits, customer order, and customer demand forecasts in ERP/APS and internal forecast tool.
- Cross functional Collaboration on forecast deltas based on actual customer demand.
- Build weekly Master Production Plan based on consensus demand plan using APS.
- Ensuring availability of raw materials by providing appropriate data to Material Planning team.
- Gather and review timely supply status with Fab execution team to ensure undisrupted supply continuity.
- Analyze WIP data to determine supply status and work through constraints or challenges to on time delivery.
- Develop and implement capacity plans to meet demand in co-ordination with Industrial Engineering team. Identify long range throughput constraints & align engineering efforts and manufacturing strategy accordingly.
- Collaborate internally with respective teams on backlog reviews or customers’ requests on order schedule changes and ensure that delivery schedules are met in a timely manner and communicated to customers and internal sales department.
- Inventory flow control by making sure customer demand is met on time.
- Collaborate with Logistics and OSATs for timely shipments of materials to meet the customer schedules.
- Analyze and resolve transactional/system issues to avoid any delays in shipment schedules.
- Work with cross functional groups (example: Yield Engineering, Customer Engineering, Turnkey Operations, OSAT Operations, Modules, Manufacturing, Sales) on production and qualification issues.
**Other Responsibilities**:
- Perform all activities in a safe and responsible manner and support all Environmental, Health, Safety & Security requirements, and programs
**Required Qualifications**:
- Education - Bachelor’s Degree in Engineering/Masters.
- Experience - bachelor's degree with 2-4 years, master's degree with 1-2 years of relevant experience in Supply chain, manufacturing, production planning, demand management, and/or business consulting
- Excellent communication, presentation, facilitation, time management, and customer relationship skills and should possess professional behavior.
- Should be well versed with Supply chain finance & revenue management
- Should have a good understanding of Supply chain planning & scheduling, Inventory management, Demand planning and forecasting
- Should have excellent analytical capabilities and presentation skills
- Should have excellent excel, advanced excel and Power BI, SQL, skills
- Basic knowledge on data extraction from database like Oracle/SAP/others.
- Should have progressive mindset towards business and responsibilities.
- Travel - (15% of travel required)
- Language Fluency - English
**Preferred Qualifications**:
- Experience with planning systems like i2 JDA/Kinaxis RR/O9 solutions/SAP IBP.etc
- Practiced in ERP systems (Oracle or SAP)
- Knowledge of Supply Chain Management and core principles (APICS Cert. or equivalent a plus)
Supply Chain Specialist
Posted today
Job Viewed
Job Description
Entity:
Customers & Products
Job Family Group:
Job Description:
- Responsible for the overall strategy and execution of the BP retail convenience supply chain management function across the U.S.
- Accountable for management of BP’s primary wholesalers (Core-Mark, McLane, and Lipari) in service of meeting contractual obligations including product supply & service levels.
- Responsible for implementing and managing corrective action(s) when wholesalers are not meeting contractual obligations.
- Management of wholesaler agreement terms requiring in-year review and action such as cost adjustments, rebate payments, allowances, service penalties, etc.
- Identify and drive continuous improvement opportunities to streamline process and improve accuracy & efficiency within the BP retail convenience supply chain.
- Responsible for ensuring that wholesalers are maintaining inventory levels in-line with forecast or sales demand including bi-monthly promotions.
- Supervising core item open purchase orders and stock status reports & expediting order fulfilment to ensure on-time delivery.
- Manage weekly reporting of contractual SLA’s/KPI’s including key items out of stocks.
- Support the category management team in reset planning and new item introduction with wholesalers.
- Responsible for managing internal and external wholesaler performance reviews.
- Problem solving and regular communication with manufacturers, wholesalers, category management, operations, and site operators (including franchisees) as needed.
- 7+ years retail supply chain management experience
- A solid understanding of wholesale contract development and management
- Retail category management or wholesale work experience a plus
- A firm understanding of supplier performance management processes (SLA’s/KPI’s)
- Experience negotiating with strategic, high dollar suppliers
- Ability to manage spontaneous (unplanned) work activity
- Strong leadership, critical thinking/analytical, and problem-solving skills
- Proficient digital literacy including Excel (VLOOKUP, pivot tables), Word, PowerPoint, and Power BI
- Works well within teams and cross-departmentally
- Very good interpersonal skills
- Self-directed
- You will work within the Merchandising Services Team which is a part of the Retail Business Support organization. The Merchandising Services Team includes approximately 25 team members supporting Price Book, Space Planning, Supply Chain, and some Retail Data Analytics activities.
- You will work closely with the US C&M business, namely Category Management, in support of driving their convenience sales and promotional plans.
- You will also work closely with BP Operations teams and BP functional teams including Procurement, Legal, and Finance.
- You will own BP’s relationship with our primary convenience wholesalers including Core-Mark, McLane, and Lipari. This means you will be the single point of accountability for ensuring that each wholesaler is servicing BP according to our contractual terms.
- This role would be great for someone who enjoys working with multiple customers, both internally and externally, and enjoys working cross-functionally to collaborate on improving the convenience supply chain.
Travel Requirement
Relocation Assistance:
Remote Type:
Skills:
Legal Disclaimer:
We are an equal opportunity employer and value diversity at our company. We do not discriminate on the basis of race, religion, color, national origin, sex, gender, gender expression, sexual orientation, age, marital status, socioeconomic status, neurodiversity/neurocognitive functioning, veteran status or disability status. Individuals with an accessibility need may request an adjustment/accommodation related to bp’s recruiting process (e.g., accessing the job application, completing required assessments, participating in telephone screenings or interviews, etc.). If you would like to request an adjustment/accommodation related to the recruitment process, please contact us .
If you are selected for a position and depending upon your role, your employment may be contingent upon adherence to local policy. This may include pre-placement drug screening, medical review of physical fitness for the role, and background checks.
Supply Chain Planner
Posted 1 day ago
Job Viewed
Job Description
As a Supply Chain Planner at Cummins, you will be responsible for planning and maintaining daily supply chain operations across one or more functional areas such as materials, production, inventory, logistics, customer service, demand management, or order fulfillment. You will ensure that both internal and external customer expectations are met through effective planning, stakeholder collaboration, and continuous process improvement.
**Key Responsibilities**
+ Develop and implement planning system strategies to enhance supply chain signals.
+ Monitor and adjust planning parameters to ensure optimal performance.
+ Execute daily operational planning processes within assigned functional areas.
+ Identify and mitigate potential supply chain failures and associated risks.
+ Collaborate with internal and external stakeholders to drive short-term tactical improvements.
+ Analyze and interpret Key Performance Indicators (KPIs) to identify improvement areas and develop action plans.
+ Participate in cross-functional process improvement initiatives.
+ Utilize planning systems and tools to ensure consistent and accurate planning signals across the supply chain.
**RESPONSIBILITIES**
**Skills and Competencies**
+ **Part Change Control Management:** Experience with supersession processes and engineering change requests.
+ **Supplier and Stakeholder Management:** Proven ability to manage relationships and expectations.
+ **Materials Planning System Utilization:** Proficient in using planning systems and tools (e.g., Excel, Access, TOAD, OMS).
+ **Plan for Every Part (PFEP):** Understanding of PFEP principles and their application across the supply chain.
+ **Master Supply Scheduling:** Ability to develop and maintain valid production schedules.
+ **Material Planning & KPI Management:** Skilled in using BI dashboards and advanced planning tools for decision-making and performance tracking.
**Core Competencies:**
+ Communicates effectively
+ Customer focus
+ Drives results
+ Global perspective
+ Manages complexity
+ Optimizes work processes
+ Values differences
**QUALIFICATIONS**
**Required Qualifications**
+ Bachelor's degree in Supply Chain Management, Business, Engineering, or a related field (or equivalent experience).
+ Certification in supply chain or logistics (e.g., APICS, CPIM) is a plus.
**Experience**
+ 5+ZW years of relevant experience in supply chain planning or a related field.
+ Experience in a manufacturing or logistics environment is preferred.
**Job** Supply Chain Planning
**Organization** Cummins Inc.
**Role Category** Hybrid
**Job Type** Exempt - Experienced
**ReqID** 2417701
**Relocation Package** No
Supply Chain Planner
Posted 6 days ago
Job Viewed
Job Description
The Supply Chain Planner is responsible for planning and maintaining daily supply chain operations in one or more functional areas such as materials, production, inventory, logistics, customer service, demand management, or order fulfillment. This role ensures that both internal and external customer expectations and requirements are consistently met through data-driven decision-making and customer-centric supply planning practices.
**Key Responsibilities**
+ Execute daily operational planning processes within a specified supply chain functional area.
+ Develop planning system strategies to enhance signal quality across the supply chain.
+ Monitor and adjust planning system parameters to improve planning accuracy and responsiveness.
+ Identify and mitigate potential supply chain risks and failures.
+ Use Kinaxis (RapidResponse or Maestro) and other planning systems/tools to drive consistent and optimized supply signals.
+ Collaborate with internal and external stakeholders to implement short-term tactical improvements.
+ Analyze Key Performance Indicators (KPIs) and develop action plans for performance improvement.
+ Participate in and support continuous improvement initiatives and cross-functional teams.
+ Leverage tools such as Advanced Planning Command Center, BI Dashboards, Excel, TOAD, and OMS for materials and capacity planning.
+ Manage engineering changes and part transitions to minimize Excess & Obsolete (E&O) inventory.
+ Apply Plan for Every Part (PFEP) methodology to ensure parts delivery efficiency.
+ Support master scheduling, inventory optimization, and replenishment planning.
**RESPONSIBILITIES**
**Skills and Experience**
+ Minimal to intermediate level of relevant supply chain planning experience.
+ Demonstrated experience in Kit Planning, E&O Management, and KPI Management.
+ Hands-on experience with Kinaxis (RapidResponse or Maestro) is strongly preferred.
+ Strong analytical skills with a data-driven approach to problem-solving.
+ Customer-centric mindset with a commitment to delivering responsive solutions.
**Key Competencies**
+ **Communicates effectively:** Delivers clear and concise messages tailored to different audiences.
+ **Customer focus:** Builds strong customer relationships and delivers tailored solutions.
+ **Drives results:** Maintains focus and performance under pressure, achieving consistent outcomes.
+ **Global perspective:** Understands broader context and considers global dynamics in decision-making.
+ **Manages complexity:** Analyzes complex information to make sound decisions.
+ **Optimizes work processes:** Continuously seeks efficient and effective process improvements.
+ **Materials Planning System Utilization:** Uses enterprise planning tools effectively to manage supply and demand.
+ **Part Change Control Management:** Manages changes to minimize supply disruptions and inventory waste.
+ **PFEP Implementation:** Applies structured planning for optimized material flow.
+ **Master Supply Scheduling:** Develops schedules aligned with customer demand and production capacity.
+ **Material Planning Expertise:** Uses advanced tools for inventory and availability decisions.
+ **Materials KPI Management:** Analyzes performance metrics and drives improvements.
+ **Values differences:** Embraces diverse perspectives to enrich team performance and innovation.
**QUALIFICATIONS**
**Required Qualifications**
+ 8+ Years of experience in Supply chain, Master production scheduling, MPS, Inventory control, Supply chain risk assessment, Excess & Obsolete (E&O) inventory, Create reports and dashboards in power BI, Data extraction, SQL.
+ Bachelor's degree in Supply Chain Management, Engineering, Business, or a related field.
+ This position may require licensing for compliance with export controls or sanctions regulations.
**Shift time - 8am to 5pm**
**Hybrid Role.**
**Job** Supply Chain Planning
**Organization** Cummins Inc.
**Role Category** Hybrid
**Job Type** Exempt - Experienced
**ReqID** 2417271
**Relocation Package** No
Be The First To Know
About the latest Industrial management Jobs in India !
Oracle Supply Chain

Posted 8 days ago
Job Viewed
Job Description
Join our team as the expert you are now and create your future.
Our clients approach us with a unique set of complex challenges to forge strategy and operations with technology. So, we are constantly on the look-out for outstanding consultants with different types of expertise and knowledge who are passionate about uncovering, untangling, and tackling the biggest challenges facing the industry. Our capable Assocciates utilize Huron tools, methodologies and best practices in the selection, planning and implementation of leading enterprise software and analytics solutions.
- Oracle Fusion SCM Consultant with expertise in at least two of the following modules: CPQ, Planning, MFG, OM, INV, Cost Management.
- Minimum of two SCM project implementations.
- Hands-on experience with BPM.
- Ability to lead fit-gap analysis, requirements gathering, documentation, application configuration, testing, and training.
- Ability to independently manage the SCM track, interact with clients, and conduct business requirement and training sessions.
- Experience conducting CRP, UAT & SIT sessions with clients/stakeholders.
- Experience in implementing SCM Cloud, configuring workflows, issue resolution, and customization across modules.
- Thorough knowledge of end-to-end P2P or O2C cycle and Supply Chain processes.
- Excellent communication and strong client-facing skills.
- Experience working with Oracle support for issue resolutions.
- Experience in SCM data upload/migration (FBDI & ADFDi) and resolving related issues.
- Experience supporting period closure activities.
- High-level knowledge of end-to-end integrations between SCM modules and other modules (e.g., Projects, Procurement, Financials, HCM).
- Strong communication, presentation, analytical, and problem-solving skills.
**Position Level**
Senior Analyst
**Country**
India
At Huron, we're redefining what a consulting organization can be. We go beyond advice to deliver results that last. We inherit our client's challenges as if they were our own. We help them transform for the future. We advocate. We make a difference. And we intelligently, passionately, relentlessly do great work.together.
Are you the kind of person who stands ready to jump in, roll up your sleeves and transform ideas into action? Then come discover Huron.
Whether you have years of experience or come right out of college, we invite you to explore our many opportunities. Find out how you can use your talents and develop your skills to make an impact immediately. Learn about how our culture and values provide you with the kind of environment that invites new ideas and innovation. Come see how we collaborate with each other in a culture of learning, coaching, diversity and inclusion. And hear about our unwavering commitment to make a difference in partnership with our clients, shareholders, communities and colleagues.
Huron Consulting Group offers a competitive compensation and benefits package including medical, dental, and vision coverage to employees and dependents; a 401(k) plan with a generous employer match; an employee stock purchase plan; a generous Paid Time Off policy; and paid parental leave and adoption assistance. Our Wellness Program supports employee total well-being by providing free annual health screenings and coaching, bank at work, and on-site workshops, as well as ongoing programs recognizing major events in the lives of our employees throughout the year. All benefits and programs are subject to applicable eligibility requirements.
Huron is fully committed to providing equal employment opportunity to job applicants and employees in recruitment, hiring, employment, compensation, benefits, promotions, transfers, training, and all other terms and conditions of employment. Huron will not discriminate on the basis of age, race, color, gender, marital status, sexual orientation, gender identity, pregnancy, national origin, religion, veteran status, physical or mental disability, genetic information, creed, citizenship or any other status protected by laws or regulations in the locations where we do business. We endeavor to maintain a drug-free workplace.
Supply Chain Manager
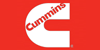
Posted 8 days ago
Job Viewed
Job Description
Lead and manage end-to-end supply chain operations across functions such as materials, production, inventory, logistics, demand management, and order fulfillment. Ensure alignment with internal and external customer expectations while driving continuous improvement and operational excellence.
**Key Responsibilities:**
+ Act as the first line of escalation for project management issues.
+ Lead weekly project management reviews with regional leads.
+ Conduct fortnightly reviews with the steering committee.
+ Oversee all operational management activities and manage a dedicated team.
+ Ensure asset management controls, including inventory accuracy.
+ Manage daily supply chain operations to ensure efficiency and reliability.
+ Lead continuous improvement initiatives aligned with Cummins Operating System.
+ Support corporate supply chain initiatives and cross-BU planning processes.
+ Collaborate with stakeholders to mitigate long-term supplier constraints.
+ Develop and implement common supply chain processes and procedures.
+ Analyze operational trends and develop corrective action plans.
+ Address supply chain failures promptly and escalate when necessary.
+ Prepare and manage annual operating plans including expenses, resources, and capital.
+ Coach and develop staff, setting goals for training, performance, and career growth.
**RESPONSIBILITIES**
**Qualifications:**
+ College, university, or equivalent degree required.
+ Licensing may be required for compliance with export controls or sanctions regulations.
**Core Competencies:**
+ **Communication:** Effectively deliver multi-mode communications tailored to diverse audiences.
+ **Talent Development:** Support career growth and organizational goals through people development.
+ **Leadership:** Provide clear direction, delegate effectively, and remove obstacles.
+ **Engagement:** Foster a motivating environment to drive organizational success.
+ **Results Orientation:** Deliver consistent outcomes even under challenging conditions.
+ **Accountability:** Uphold commitments and ensure others do the same.
+ **Trust Building:** Demonstrate integrity and authenticity to gain confidence.
+ **Process Optimization:** Continuously improve work processes for efficiency and effectiveness.
**Technical Competencies:**
+ **Inventory Management & Optimization:** Use analytics to determine optimal inventory levels across the supply chain.
+ **Material Planning:** Utilize advanced tools (e.g., BI dashboards, planning centers) for inventory decisions and root cause analysis.
+ **Materials KPI Management:** Interpret KPIs to assess performance and drive strategic improvements.
+ **Supply Chain Knowledge:** Understand and influence end-to-end supply chain integration balancing inventory, cost, and delivery.
+ **Values Differences:** Embrace diverse perspectives and cultures to enrich organizational outcomes.
**QUALIFICATIONS**
**Skills and Experience:**
+ **Experience:** 15 years of relevant supply chain or operations management experience.
+ **Shift Requirement:** Must be willing to work night shifts to support US time zone operations.
**Location:** **Pune, Maharashtra (Night Shift: 5 PM to 2 AM IST)**
**Shift Benefits:** Night shift allowance, pickup and drop facilities within PMC & PCMC jurisdict
**Job** Supply Chain Planning
**Organization** Cummins Inc.
**Role Category** Hybrid
**Job Type** Exempt - Experienced
**ReqID** 2416935
**Relocation Package** No
Supply Chain Analyst
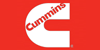
Posted 8 days ago
Job Viewed
Job Description
The Supply Chain Analyst utilizes analytical and quantitative methods to understand, predict, and enhance supply chain processes. This role supports Cummins' supply chain by analyzing performance, identifying areas for improvement, and providing actionable recommendations. The analyst will also offer coordination support to stakeholders and suppliers, primarily for the US time zone.
**Key Responsibilities:**
+ Coordinate with internal and external suppliers and cross-functional stakeholders.
+ Process and monitor purchase orders to suppliers, ensuring alignment with the supply plan.
+ Monitor and adjust procurement signals and expedite parts as necessary.
+ Analyze key performance indicators (KPIs) and supply chain metrics to identify trends and improvement opportunities.
+ Provide repeatable and scalable analytics and reporting through existing business systems.
+ Ensure accuracy and integrity of data across all supply chain reports and analytics.
+ Participate in continuous improvement and Six Sigma projects.
+ Support inventory management and planning efforts using advanced planning tools such as Xelus, GOMS, and aftermarket material planning systems.
**RESPONSIBILITIES**
**Competencies:**
+ **Communicates effectively** - Delivers clear and concise messages tailored to varied audiences.
+ **Drives results** - Demonstrates a track record of achieving and exceeding goals.
+ **Global perspective** - Considers international implications and best practices in supply chain decisions.
+ **Manages complexity** - Synthesizes large amounts of data and information to solve problems.
+ **Optimizes work processes** - Continuously improves processes for efficiency and quality.
+ **Values differences** - Embraces diversity of thought and culture to drive better outcomes.
**Technical Skills:**
+ **Materials Planning System Utilization** - Operates planning tools to manage supply/demand, using root cause analysis for resolution.
+ **Plan for Every Part (PFEP)** - Applies PFEP principles to optimize part flow and inventory.
+ **Inventory Management and Optimization** - Leverages algorithms and analysis to recommend optimal inventory strategies.
+ **Material Planning** - Uses advanced planning tools for inventory optimization and root cause analysis.
+ **Materials KPI Management** - Interprets and acts on supply chain KPIs to drive performance.
**Additional Information:**
+ This role requires working during US business hours (5 PM - 2 AM IST).
+ Night shift allowance and transportation facilities are provided.
+ Candidates must be willing and able to operate independently and as part of a global team.
**Work Schedule:** Night Shift (5:00 PM to 2:00 AM IST)
**Shift Benefits:** Night Shift Allowance; Pickup and Drop facilities within PMC & PCMC jurisdiction
**QUALIFICATIONS**
**Required Qualifications:**
+ College, university, or equivalent degree in Supply Chain, Engineering, Business, or a related field.
+ This position may require licensing for compliance with export controls or sanctions regulations.
**Skills and Experience:**
+ 1 to 3 years of experience in supply chain, procurement, inventory management, or logistics.
+ Exposure to or hands-on experience with planning tools such as Xelus, GOMS, or other ERP/MRP systems.
+ Strong data analysis and troubleshooting capabilities using Excel, Access, BI dashboards, etc.
+ Experience in working night shifts or with US-based operations is a plus.
**Job** Supply Chain Planning
**Organization** Cummins Inc.
**Role Category** Hybrid
**Job Type** Exempt - Experienced
**ReqID** 2415711
**Relocation Package** No