240 Chemical Engineering jobs in India
Process Safety Engineer - TSI
Posted 1 day ago
Job Viewed
Job Description
Entity:
Production & Operations
Job Family Group:
Job Description:
bp Technical Solutions India (TSI) center in Pune, strives to build on bp’s existing engineering and technical strengths to deliver high quality services to its hydrocarbons and new energy businesses worldwide. TSI brings together diverse engineering capability to provide technical services across a range of areas including engineering, maintenance, optimization, data processes, projects and subsurface, to deliver safe, affordable and lower emission energy, while continuously innovating how we work.
At bp, we’re reimagining energy for people and our planet. We’re leading the way in reducing carbon emissions and developing more balanced methods for solving the energy challenge. We’re a team with multi-layered strengths of engineers, scientists, traders and business professionals determined to find answers to problems.
And we know we can’t do it alone. We’re looking for people who share our passion for reinvention, to bring fresh opinions, ambition, and to challenge our thinking in our goal to achieve net zero!
Let me tell you about the role Role Synopsis:The Process Safety Engineer will join the Production & Operations (P&O) Projects India organisation in the engineering and quality team to provide engineering expertise, oversight, judgment and support to Production & Operations (P&O) Projects.
The role is based at the Pune office but will require significant contractor facing work at major engineering contractor office locations in both India and possibly ex-India.
What you will deliverSupport the development of the technical scope of project options to ensure selection and progression of safe, competitive and robust projects
Support Process Safety engineering activity on the projects in support of an Inherently Safer Design (ISD) and application of specific safety features developed during the project phases
Provide technical guidance and advice to the Project team; support technical and engineering scope development and decision making with process safety impacts
Develop and implement Process Safety Philosophy for projects in cooperation with the contractors
Develop and implement the Design Hazard Management Plan for projects
Provide verification of key process safety deliverables by engineering contractors in terms of quality and conformance with project requirements; provide oversight of performance of contractor for process safety scope
Using prescribed BP approved design methods and procedures, support preparation of and participate in key areas such as HAZOP, LOPA, HAZID and environmental reviews where necessary
Consult with project team, Technical Authorities and functional specialists as appropriate on key issues of risk, engineering integrity, project specifications and significant issues of potential exceptions/non-compliance
Maintain knowledge of codes, standards, and regulations relevant to process systems and process safety; ensure deviations from BP standards, project specifications and processes are identified, justified and deviations processed in accordance with appropriate procedures
Work with process safety functional support and third-party consultants as necessary to support assurance and design.What you will need to be successful
Bachelor’s Degree in Chemical Engineering or equivalent
Working towards Chartered Engineer or Registered Professional Engineer or equivalent
Minimum 5+ years in oil and gas/petrochemical/ refining/ chemical or equivalent, with minimum 2 years' experience of relevant process safety engineering work in Large scale Capital projects.
Experience in design safety in Front End Engineering Design (FEED) and Detailed Design stages of major projects
Experience in the oil and gas industry
Experience in the technical safety system design such as firewater, lifesaving equipment selection, and fire and gas detector layout and mapping
Experience working with third party design contractors
Knowledge of stage gated project processes
Knowledge of engineering practices and codes and standards
Good understanding of incorporating inherently safer design principles into design
Track record of consistent delivery and able to demonstrate effective communication and influence with all levels of the project team, engineering contractors and project leadership
Demonstrated ability to foster effective teamwork across multiple locations, teams, and other engineering disciplines
Good to have experiences/skills (Can be trained for – learning/on-the-job):
Experience in working in concept selection stage of projects
Experience working under a range of Contracting models (reimbursable, lump sum, etc.)
Experience managing engineering contractor performance
General knowledge of gas processing, refining or petrochemical processes and typical flow schemes
Experience with process safety modelling, application and result interpretation of results for use by design teams (e.g. fire hazard assessment, dispersion modelling, quantitative risk assessment)
A self-starter and pragmatic decision maker, willing to challenge and ensure engineering value is delivered.
Be self-motivated with a willingness to learn from others and work with minimum direction
Excellent interpersonal and leadership skills
You will work with
Project Engineering Manager
Engineering Contractor(s)
Process & Process Safety Engineering Team
Other bp Discipline Engineers
Projects Commissioning and Start-up teams
Operations & Maintenance teams
Quality team
Working hours to be standard (9 AM to 6 PM)
% travel requirementsUp to 50% (this is high time at contractors, typically 3 days / week, or assignment to be co-located in contractor offices.
At bp, we provide the following environment & benefits to you:
Life & health insurance, medical care packageFlexible working schedule: home office up to 2 days / week, based on team agreement
Opportunity to build up a long-term career path and develop your skills with a wide range of learning options
Family friendly workplace e.g.: parental leave, Mother-baby roomEmployees’ wellbeing programs e.g.: Employee Assistance Program, Company Recognition Program
Possibility to join our social communities and networksAssets like phone and company laptop are provided from the first day of employment with other equipment if requested
Why Join our team?
At bp, we support our people to learn and grow in a diverse and challenging environment. We believe that our team is strengthened by diversity. We are committed to crafting an inclusive environment in which everyone is respected and treated fairly. Diversity Statement: At bp, we provide an excellent environment and benefits such as an open and inclusive culture, a great work-life balance, tremendous learning and development opportunities to craft your career path, life and health insurance, medical care package and many others!
Diversity sits at the heart of our company and as an equal opportunity employer, we stay true to our mission by ensuring that our place can be anyone's place. We do not discriminate based on race, religion, colour, national origin, gender and gender identity, sexual orientation, age, marital status, veteran status or disability status. We will ensure that individuals with disabilities are provided reasonable accommodation to participate in the job application and interview process, to perform crucial job functions, and to receive other benefits and privileges of employment.
Travel Requirement
Relocation Assistance:
Remote Type:
Skills:
Legal Disclaimer:
We are an equal opportunity employer and value diversity at our company. We do not discriminate on the basis of race, religion, color, national origin, sex, gender, gender expression, sexual orientation, age, marital status, socioeconomic status, neurodiversity/neurocognitive functioning, veteran status or disability status. Individuals with an accessibility need may request an adjustment/accommodation related to bp’s recruiting process (e.g., accessing the job application, completing required assessments, participating in telephone screenings or interviews, etc.). If you would like to request an adjustment/accommodation related to the recruitment process, please contact us .
If you are selected for a position and depending upon your role, your employment may be contingent upon adherence to local policy. This may include pre-placement drug screening, medical review of physical fitness for the role, and background checks.
Senior Process Safety Engineer-Site Projects-TSI
Posted 1 day ago
Job Viewed
Job Description
Entity:
Production & Operations
Job Family Group:
Job Description:
About bp
bp Technical Solutions India (TSI) center in Pune, strives to build on bp’s existing engineering and technical strengths to deliver high quality services to its hydrocarbons and new energy businesses worldwide. TSI brings together diverse engineering capability to provide technical services across a range of areas including engineering, maintenance, optimization, data processes, projects and subsurface, to deliver safe, affordable and lower emission energy, while continuously innovating how we work.
At bp, we’re reimagining energy for people and our planet. We’re leading the way in reducing carbon emissions and developing more balanced methods for solving the energy challenge. We’re a team with multi-layered strengths of engineers, scientists, traders and business professionals determined to find answers to problems.
And we know we can’t do it alone. We’re looking for people who share our passion for reinvention, to bring fresh opinions, ambition, and to challenge our thinking in our goal to achieve net zero!
Let me tell you about the role
The Process Safety Engineer provides support to Site Projects to help ensure compliance with applicable regulations and help manage and reduce process safety risk. The Process Safety Engineer will be actively involved with regulatory required process hazard analysis and management of change activities to help ensure risks are identified and managed.
Provision of deep process safety engineering expertise and judgment in service of the assets, working closely with Site Projects Engineering Managers to ensure efficient handover of all issues that require engineering input to resolve. Ensure pragmatic solutions are implemented for management of risk, production efficiency improvement, maintenance, defect elimination and engineering standardization in support of safe, reliable and compliant operations.
What you will deliver
Provides process safety expertise to other teams by performing and reviewing complex, or non-routine process safety engineering calculations and analysis including dispersion modelling
Support development of Process Design Basis / Project Safety Philosophies
Provides process safety expertise to MoCs, brownfield projects and modifications, hazard identification and risk assessment processes
Collaborates seamlessly to review deliverables from external contractors and vendors to meet project baseline and bp requirements.
Provides process safety expertise to delivery of regional projects and leads on resolution of complex, multi-discipline technical issues where the dominant component is process or process safety related
Records relevant learnings in shared learning systems, incorporates into local activities and escalates high priority lessons
Ensures compliance and audit requirements are met for all responsible activities.
What you will need to be successful
Must have educational qualifications:
Degree in Chemical Engineering or equivalent
Must have certifications: NA
Preferred education/certifications:
Chartered Engineer or Professional Engineer or equivalent
Minimum years of relevant experience:
10 years in oil and gas/petrochemical or equivalent oil and gas, petrochemical, refining and chemical industry
Total years of experience :
15-20 Years
Must have experiences/skills (To be hired with):
Ability to manage contractors on behalf of bp
Experience with facilitation of HAZIDs
Experience with facilitation of HAZOP/LOPA
Experience with facilitation of What-Ifs
Extensive technical understanding of process engineering, understanding of process modelling tools
Good understanding of risk management including the use of risk barrier diagrams processes in the oil and gas industry
Proven ability in practical application of engineering standards and practices for process engineering
Ability to manage safety across all stages of the project design process
Fluent in English - written and oral-Conversant with industry standards on Process Safety Engineering
Delivery focused and able to demonstrate effective project technical management skills
Ability to establish strong working relationships across a global community
Ability and confidence to engage with and influence senior leadership on technical matters
Good to have experiences/skills (Can be trained for – learning/on-the-job):
Experience of working in a remote team with a collaborative approach to delivery
Track record of engaging, influencing and leading across teams and functions to deliver engineering improvements centrally
Passion for Excellence in Project Delivery and Continuous Improvement
Pragmatic decision maker, willing to challenge and ensure engineering value is delivered
Self-motivated, delivery focused with a willingness to learn from others and work with minimum direction
You will work with
Operations personnel
Refinery and Production Teams
Projects Team
External contractors/vendors
Shift
Working hours (India/US Shift 1400-2300) to support Business Partners
% travel requirements
10%
Why Join our team?
At bp, we support our people to learn and grow in a diverse and challenging environment. We believe that our team is strengthened by diversity. We are committed to crafting an inclusive environment in which everyone is respected and treated fairly. Diversity Statement: At bp, we provide an excellent environment and benefits such as an open and inclusive culture, a great work-life balance, tremendous learning and development opportunities to craft your career path, life and health insurance, medical care package and many others!
Diversity sits at the heart of our company and as an equal opportunity employer, we stay true to our mission by ensuring that our place can be anyone's place. We do not discriminate based on race, religion, colour, national origin, gender and gender identity, sexual orientation, age, marital status, veteran status or disability status. We will ensure that individuals with disabilities are provided reasonable accommodation to participate in the job application and interview process, to perform crucial job functions, and to receive other benefits and privileges of employment.
Travel Requirement
Relocation Assistance:
Remote Type:
Skills:
Legal Disclaimer:
We are an equal opportunity employer and value diversity at our company. We do not discriminate on the basis of race, religion, color, national origin, sex, gender, gender expression, sexual orientation, age, marital status, socioeconomic status, neurodiversity/neurocognitive functioning, veteran status or disability status. Individuals with an accessibility need may request an adjustment/accommodation related to bp’s recruiting process (e.g., accessing the job application, completing required assessments, participating in telephone screenings or interviews, etc.). If you would like to request an adjustment/accommodation related to the recruitment process, please contact us .
If you are selected for a position and depending upon your role, your employment may be contingent upon adherence to local policy. This may include pre-placement drug screening, medical review of physical fitness for the role, and background checks.
Process Safety Engineer (Open Recommendation Squad) - TSI
Posted 1 day ago
Job Viewed
Job Description
Entity:
Production & Operations
Job Family Group:
Job Description:
bp Technical Solutions India (TSI) center in Pune, strives to build on bp’s existing engineering and technical strengths to deliver high quality services to its hydrocarbons and new energy businesses worldwide. TSI brings together diverse engineering capability to provide technical services across a range of areas including engineering, maintenance, optimization, data processes, projects and subsurface, to deliver safe, affordable and lower emission energy, while continuously innovating how we work.
At bp, we’re reimagining energy for people and our planet. We’re leading the way in reducing carbon emissions and developing more balanced methods for solving the energy challenge. We’re a team with multi-layered strengths of engineers, scientists, traders and business professionals determined to find answers to problems.
And we know we can’t do it alone. We’re looking for people who share our passion for reinvention, to bring fresh opinions, ambition, and to challenge our thinking in our goal to achieve net zero!
Let me tell you about the role The role acts as a central resource for safe, reliable and compliant closure of HAZOP/LOPA recommendations created by bp’s centralized HAZOP/LOPA Revalidation program. What you will deliver
Performance management of assigned HAZOP/LOPA recommendation items and their associated path to closure
Apply a wide range of process and process safety engineering techniques to continuously reduce risk at bp’s operations in Production and Refining
Create lessons learned and apply best practices for identifying risk scenarios and interface with the central HAZOP/LOPA delivery team to incorporate those learnings proactively What you will need to be successful Must have educational qualifications:
Degree in Chemical Engineering or equivalent Must have certifications: NA Preferred education/certifications:
Chartered Engineer or Professional Engineer or equivalent Minimum years of relevant experience:
8 years in oil and gas/petrochemical or equivalent oil and gas, petrochemical, refining and chemical industry Total years of experience:
8-15 Years Must have experiences/skills (To be hired with):
Extensive technical understanding of process engineering, understanding of process and process safety modelling tools, good understanding of risk management including the use of risk barrier diagrams processes in the oil and gas industry
Experience adding sizing cases to flare and relief analysis
Experience with consequence modelling
Proven ability in practical application of engineering standards and practices for process engineering
Fluent in written and oral English with industry standards on Process Safety Engineering
Delivery focused and able to demonstrate effective project technical management skills
Ability to establish strong working relationships across a global community
Ability and confidence to engage with and influence senior leadership on technical matters
Past experience with HAZOP/LOPA (including understanding how recommendations are created)
Proven track record delivering a Process Safety Program Good to have experiences/skills (Can be trained for – learning/on-the-job):
Experience of working in a remote team with a collaborative approach to delivery
A proven record of accomplishment in risk management and contractor performance management
Track record of engaging, influencing, and leading across teams and functions to deliver engineering improvements centrally
Passion for Excellence in Project Delivery and Continuous Improvement
Pragmatic decision maker, willing to challenge and ensure engineering value is delivered
Self-motivated, delivery focused with a willingness to learn from others and work with minimal direction You will work with
Operations personnel
Refinery Teams
Region Teams
% Travel requirements 10%
At bp, we provide the following environment & benefits to you:
Life & health insurance, medical care package
Flexible working scehedule: home office up to 2 days / week, based on team agreement
Opportunity to build up long term career path and develop your skills with wide range of learning options
Family friendly workplace e.g.: parental leave, Mother-baby room Employees’ wellbeing programs e.g.: Employee Assistance Program, Company Recognition
Program Confidential Possibility to join our social communities and networks Assets like phone and company laptop are provided from the first day of employment with other equipment if requested
Why Join our team?
At bp, we support our people to learn and grow in a diverse and challenging environment. We believe that our team is strengthened by diversity. We are committed to crafting an inclusive environment in which everyone is respected and treated fairly. Diversity Statement: At bp, we provide an excellent environment and benefits such as an open and inclusive culture, a great work-life balance, tremendous learning and development opportunities to craft your career path, life and health insurance, medical care package and many others!
Diversity sits at the heart of our company and as an equal opportunity employer, we stay true to our mission by ensuring that our place can be anyone's place. We do not discriminate based on race, religion, colour, national origin, gender and gender identity, sexual orientation, age, marital status, veteran status or disability status. We will ensure that individuals with disabilities are provided reasonable accommodation to participate in the job application and interview process, to perform crucial job functions, and to receive other benefits and privileges of employment.
Travel Requirement
Relocation Assistance:
Remote Type:
Skills:
Legal Disclaimer:
We are an equal opportunity employer and value diversity at our company. We do not discriminate on the basis of race, religion, color, national origin, sex, gender, gender expression, sexual orientation, age, marital status, socioeconomic status, neurodiversity/neurocognitive functioning, veteran status or disability status. Individuals with an accessibility need may request an adjustment/accommodation related to bp’s recruiting process (e.g., accessing the job application, completing required assessments, participating in telephone screenings or interviews, etc.). If you would like to request an adjustment/accommodation related to the recruitment process, please contact us .
If you are selected for a position and depending upon your role, your employment may be contingent upon adherence to local policy. This may include pre-placement drug screening, medical review of physical fitness for the role, and background checks.
Senior Process Safety Engineer - TSI
Posted 1 day ago
Job Viewed
Job Description
Entity:
Production & Operations
Job Family Group:
Job Description:
bp Technical Solutions India (TSI) center in Pune, strives to build on bp’s existing engineering and technical strengths to deliver high quality services to its hydrocarbons and new energy businesses worldwide. TSI brings together diverse engineering capability to provide technical services across a range of areas including engineering, maintenance, optimization, data processes, projects and subsurface, to deliver safe, affordable and lower emission energy, while continuously innovating how we work.
At bp, we’re reimagining energy for people and our planet. We’re leading the way in reducing carbon emissions and developing more balanced methods for solving the energy challenge. We’re a team with multi-layered strengths of engineers, scientists, traders and business professionals determined to find answers to problems.
And we know we can’t do it alone. We’re looking for people who share our passion for reinvention, to bring fresh opinions, ambition, and to challenge our thinking in our goal to achieve net zero!
Let me tell you about the role
The Senior Process Safety Engineer will join the Projects India organisation in the engineering and quality team to provide engineering expertise, oversight, judgment and support to Production & Operations (P&O) Projects.
The role is based at the Pune office but will require significant contractor facing work at major engineering contractor office locations in both India and possibly ex-India.
What you will deliver
Support the development of the technical scope of project options to ensure selection and progression of safe, competitive and robust projects
Be responsible for Process Safety engineering activity on the projects in support of an Inherently Safer Design (ISD) and application of specific safety features developed during the project phases
Provide technical guidance and advice to the Project team; support technical and engineering scope development and decision making with process safety impacts
Develop and implement Process Safety Philosophy for projects in cooperation with the contractors
Develop and implement the Design Hazard Management Plan for projects
Manage the delivery of Process Safety deliverables; provide verification of key process safety deliverables by engineering contractors in terms of quality and conformance with project requirements; provide oversight of performance of contractor for process safety scope
Prescribe appropriate BP approved design methods and procedures, support preparation and participate in key areas such as HAZOP, LOPA, HAZID and environmental reviews where necessary; assist project teams in application
Consult with project team, Technical Authorities and functional specialists as appropriate on key issues of risk, engineering integrity, project specifications and significant issues of potential exceptions/non-compliance
Maintain knowledge of codes, standards, and regulations relevant to process systems and process safety; ensure deviations from BP standards, project specifications and processes are identified, justified and deviations processed in accordance with appropriate procedures
Engage and manage process safety functional support and third-party consultants as necessary to support assurance and design
Support process safety capability and competence through the active mentoring, coaching and training of other process safety engineers.
What you will need to be successful
Must have educational qualifications:
Bachelor’s Degree in Chemical Engineering or equivalent
Preferred education/certifications:
Chartered Engineer or Registered Professional Engineer
Minimum years of relevant experience:
Minimum 12+ years in oil and gas/petrochemical/ refining/ chemical or equivalent, with minimum 5 years’ experience of leading process safety and HSSE in design engineering work in Major Capital projects.
Must have experiences/skills (To be hired with):
Experience in design safety in Front End Engineering Design (FEED) and Detailed Design stages of major projects
Experience in the oil and gas industry
Experience working in a discipline leadership role, managing engineering contractor performance
Experience in the technical safety system design such as firewater, lifesaving equipment selection, and fire and gas detector layout and mapping
Experience with process safety modelling, application and result interpretation of results for use by design teams (e.g. fire hazard assessment, dispersion modelling, quantitative risk assessment)
Knowledge of stage gated project processes
Knowledge of engineering practices and codes and standards
Good understanding of incorporating inherently safer design principles into design
Track record of consistent delivery and able to demonstrate effective project technical management and leadership skills
Demonstrated ability to effectively communicate and influence with all levels of the project team, engineering contractors and project leadership
Demonstrated ability to foster effective teamwork across multiple locations, teams, and other engineering disciplines
Good to have experiences/skills (Can be trained for – learning/on-the-job):
Experience in working in concept selection stage of projects
Experience working under a range of Contracting models (reimbursable, lump sum, etc)
General knowledge of gas processing, refining or petrochemical processes and typical flow schemes
A self-starter and pragmatic decision maker, willing to challenge and ensure engineering value is delivered
Be self-motivated with a willingness to learn from others and work with minimum direction
Excellent interpersonal and leadership skills and ability to lead through influencing others
You will work with
Project Engineering Manager
Engineering Contractor(s)
Process & Process Safety Engineering Team
Other bp Discipline Engineers
Projects Commissioning and Start-up teams
Operations & Maintenance teams
Quality team
Shift
Working hours to be standard (9 AM to 6 PM)
% travel requirements
Up to 50% (this is high time at contractors, typically 3 days / week, or assignment to be co-located in contractor offices.
At bp, we provide the following environment & benefits to you:
Life & health insurance, medical care package
Flexible working schedule: home office up to 2 days / week, based on team agreement
Opportunity to build up a long-term career path and develop your skills with a wide range of learning options
Family friendly workplace e.g.: parental leave, Mother-baby room
Employees’ wellbeing programs e.g.: Employee Assistance Program, Company Recognition Program
Possibility to join our social communities and networks
Assets like phone and company laptop are provided from the first day of employment with other equipment if requested
Why Join our team?
At bp, we support our people to learn and grow in a diverse and challenging environment. We believe that our team is strengthened by diversity. We are committed to crafting an inclusive environment in which everyone is respected and treated fairly. Diversity Statement: At bp, we provide an excellent environment and benefits such as an open and inclusive culture, a great work-life balance, tremendous learning and development opportunities to craft your career path, life and health insurance, medical care package and many others!
Diversity sits at the heart of our company and as an equal opportunity employer, we stay true to our mission by ensuring that our place can be anyone's place. We do not discriminate based on race, religion, colour, national origin, gender and gender identity, sexual orientation, age, marital status, veteran status or disability status. We will ensure that individuals with disabilities are provided reasonable accommodation to participate in the job application and interview process, to perform crucial job functions, and to receive other benefits and privileges of employment.
Travel Requirement
Relocation Assistance:
Remote Type:
Skills:
Legal Disclaimer:
We are an equal opportunity employer and value diversity at our company. We do not discriminate on the basis of race, religion, color, national origin, sex, gender, gender expression, sexual orientation, age, marital status, socioeconomic status, neurodiversity/neurocognitive functioning, veteran status or disability status. Individuals with an accessibility need may request an adjustment/accommodation related to bp’s recruiting process (e.g., accessing the job application, completing required assessments, participating in telephone screenings or interviews, etc.). If you would like to request an adjustment/accommodation related to the recruitment process, please contact us .
If you are selected for a position and depending upon your role, your employment may be contingent upon adherence to local policy. This may include pre-placement drug screening, medical review of physical fitness for the role, and background checks.
Chemical Engr II
Posted 8 days ago
Job Viewed
Job Description
You will be an integrated network of technical professionals working together to provide outstanding technical insights. Customer Value is the GSC's key result to ensure we generate relevant insights from the extracted data for improved outcomes.
+ Be agile, innovating, and customer focused.
+ Review operations with customers and assisting with defining and quantifying customer benefits
+ Monitoring different UOP technologies process and identifying areas for improvement/optimization and assets requiring enhanced focus.
+ Provide readily available technical solutions/ work to get the solution to our customers.
+ Initial triage of technical issues with the escalation process to TS.
+ Proactively communicate insights from trends, establish patterns, diagnostic investigations, and solutions to prevent future issues.
+ Ensure upkeep of all solutions by troubleshooting the PM/PTA/PRA/POA/Benchmarking /Future Solutions on time to ensure high on-screen availability of the running solutions
+ Apply data mining to handle unstructured data to derive technical insights.
+ Perform descriptive and inferential statistics to summarize datasets.
+ Derive problem statement from ambiguous data, create a hypothesis, use analytics technology and tools to test hypothesis and form conclusions
+ Analysis of large amounts of historical data, determining suitability for modeling, data clean-up and filtering, pattern identification and variable creation, applying automated predictive analytics.
+ The focus is to support product, system, and solution through designing and developing pipelines.
+ Work with the team to innovate - next-generation BIG DATA monitoring tools (Analytics using exception-based /Artificial Intelligence/Machine Learning) and build an operation dashboard for the GSC's sustainability & efficient operation.
+ Align with the Intention of the LST Business and ensure collective commitment for the GSC's Key results.
+ Part of 24* 7 Operation of GSCCC Digital Insight
+ Working in 24*7 Shift is an integral part of this role. Work with GSCCC Operation leader closely to make GSC as Center of Excellence
**Basic Candidate Qualification:**
- BS degree in Chemical Engineering
**Additional Candidate Qualifications:**
+ Passion for visualizing hidden relationships in technical data with ProSight
+ Excellent verbal, written, interpersonal communication & effective presentation skills
+ English language (oral and written)
+ Ability to multi-task
+ Be flexible to come in shift as a replacement in short notice
+ Effective presentation, and communication skills
+ Continuous learning and research-oriented mindset. Ability to think out of the box: Ability to come up with bright ideas and always looking at the next big thing in technology.
+ Have strong analytical skills; be able to interpret data, identify trends, and make suggestions for improvements
+ Knowledge of DataScience Open Source is added plus.
+ Proficiency in computer applications with emphasis on Data Analytics & Data Science is desirable
+ Creative approach to process development and customer-centric behavior
+ Comprehensive analytical, troubleshooting & problems solving skills.
+ Ability to work independently and in a team environment, focusing strongly on delivering SMART data results and identifying alternative solutions when challenges arise from unstructured data.
+ Ability to define the problem with limited information
+ This role may require global customer-facing and internal/external travel, up to 10% of the time.
Honeywell helps organizations solve the world's most complex challenges in automation, the future of aviation and energy transition. As a trusted partner, we provide actionable solutions and innovation through our Aerospace Technologies, Building Automation, Energy and Sustainability Solutions, and Industrial Automation business segments - powered by our Honeywell Forge software - that help make the world smarter, safer and more sustainable.
Honeywell is an equal opportunity employer. Qualified applicants will be considered without regard to age, race, creed, color, national origin, ancestry, marital status, affectional or sexual orientation, gender identity or expression, disability, nationality, sex, religion, or veteran status.
Lead Chemical Engr
Posted 8 days ago
Job Viewed
Job Description
This position will be the key leadership position to look after 24x7 operations at Global Solutions Command and Control Center.
+ Be agile, innovative, and customer focused.
+ Lead Global Solutions Center, day to day operations with strong operation MOS.
+ This role will be key in balancing the resource and priority items based on SIOP meetings.
+ This position is the key to ensuring seamless operation and accountability of 24x7 decision making.
+ Ensuring high resource utilization/billability of the center.
+ Accountable to minimize manual work by Automation/Standardization.
+ Lead the automation initiative and technical decision making for the center based on business needs/priorities.
+ Monitoring different UOP technologies process and identifying areas for improvement/optimization and assets requiring enhanced focus.
+ Provide readily available technical solutions / work to get the solution to our customers.
+ Initial triage of technical issues with the escalation process to TS.
+ Proactively communicate insights from trends, establish patterns, diagnostic investigations, and solutions to prevent future issues.
+ Ensure upkeep of all solutions by troubleshooting the PM/PTA/Exception Based Alerts/Benchmarking /Future Solutions on time to ensure high on-screen availability of the running solutions
+ Expertise in doing Exploratory Data Analysis on Time series data using ProSight.
+ Hands-on skills in developing insights end-to-end, including EDA, data processing, hyper-parameter tuning, baseline modeling, and model deployment.
+ Apply data mining to handle unstructured data to derive technical insights.
+ Perform descriptive and inferential statistics to summarize datasets.
+ Prior knowledge of Time Series Forecasting in Prosight/Data Science.
+ Knowledge of UOP Technologies.
+ Derive problem statement from ambiguous data, create a hypothesis, use analytics and tools to test hypothesis and form conclusions
+ Excellent technical expertise in all the areas of Descriptive, Predictive, and Prescriptive Analytics, including Optimization Analytics, Simulation & Advanced Machine Learning Algorithms.
+ Experience in cleaning, process, manipulate, and analyze data.
+ Ability to build scalable, user-centric applications -Building Models Data Science
+ Analysis of large amounts of historical data, determining suitability for modeling, data clean-up and filtering, pattern identification and variable creation, applying automated predictive analytics.
+ The focus is to support product, system, and solution through designing and developing pipelines.
+ Establishing additional work processes & documentation for the GSC.
+ Work with team to remove gaps in current solutions/tools to guide future development efforts with ProSight (UOP Internal platform) & content of solutions.
+ Work with the team to innovate - next-generation BIG DATA monitoring tools (Analytics using exception-based /Artificial Intelligence/Machine Learning) and work on operation dashboard for the GSC's sustainability & efficient operation.
+ Align with the Intention of the LST Business and ensure collective commitment for the GSC's Key results.
+ Part of 24x7 Operation of GSCCC Digital Insight
+ Working in 24x7 Shift is an integral part of this role. Work with GSCCC Center leader closely to make GSC as "Center of Excellence"
**Basic Candidate Qualification:**
- Bachelor's degree in chemical engineering
- Min of 12 years of experience in technical service or process operation/engineering/monitoring role within the refining and petrochemical industry.
**Additional Candidate Qualifications:**
+ Passion for visualizing hidden relationships in technical data with ProSight
+ Must demonstrate leadership to respond to customers seeking an urgent resolution to sometimes ambiguous technical needs quickly gain the Customer's trust and show accountability for problem resolution.
+ Excellent verbal, written, interpersonal communication & effective presentation skills
+ English language (oral and written)
+ Ability to multi-task
+ Be flexible to come in shift as a replacement in short notice
+ Exposure to techniques like forecasting, predictive methods, classification techniques, and segmentation is highly desirable.
+ Effective project management, presentation, and communication skills
+ Continuous learning and research-oriented mindset. Ability to think out of the box: Ability to come up with bright ideas and always looking at the next big thing in technology.
+ Have strong analytical skills; be able to interpret data, identify trends, and make suggestions for improvements
+ Knowledge of DataScience Open Source is added plus.
+ Proficiency in computer applications with emphasis on Data Analytics & Data Science is desirable
+ Creative approach to process development and customer-centric behavior
+ Comprehensive analytical, troubleshooting & problems solving skills.
+ Ability to work independently and in a team environment, focusing strongly on delivering SMART data results and identifying alternative solutions when challenges arise from unstructured data.
+ Ability to define the problem with limited information
+ This role may require global customer-facing and internal/external travel, up to 10% of the time.
Honeywell helps organizations solve the world's most complex challenges in automation, the future of aviation and energy transition. As a trusted partner, we provide actionable solutions and innovation through our Aerospace Technologies, Building Automation, Energy and Sustainability Solutions, and Industrial Automation business segments - powered by our Honeywell Forge software - that help make the world smarter, safer and more sustainable.
Honeywell is an equal opportunity employer. Qualified applicants will be considered without regard to age, race, creed, color, national origin, ancestry, marital status, affectional or sexual orientation, gender identity or expression, disability, nationality, sex, religion, or veteran status.
Lead Chemical Engr
Posted 8 days ago
Job Viewed
Job Description
This position will be the key leadership position to look after 24x7 operations at Global Solutions Command and Control Center.
+ Be agile, innovative, and customer focused.
+ Lead Global Solutions Center, day to day operations with strong operation MOS.
+ This role will be key in balancing the resource and priority items based on SIOP meetings.
+ This position is the key to ensuring seamless operation and accountability of 24x7 decision making.
+ Ensuring high resource utilization/billability of the center.
+ Accountable to minimize manual work by Automation/Standardization.
+ Lead the automation initiative and technical decision making for the center based on business needs/priorities.
+ Monitoring different UOP technologies process and identifying areas for improvement/optimization and assets requiring enhanced focus.
+ Provide readily available technical solutions / work to get the solution to our customers.
+ Initial triage of technical issues with the escalation process to TS.
+ Proactively communicate insights from trends, establish patterns, diagnostic investigations, and solutions to prevent future issues.
+ Ensure upkeep of all solutions by troubleshooting the PM/PTA/Exception Based Alerts/Benchmarking /Future Solutions on time to ensure high on-screen availability of the running solutions
+ Expertise in doing Exploratory Data Analysis on Time series data using ProSight.
+ Hands-on skills in developing insights end-to-end, including EDA, data processing, hyper-parameter tuning, baseline modeling, and model deployment.
+ Apply data mining to handle unstructured data to derive technical insights.
+ Perform descriptive and inferential statistics to summarize datasets.
+ Prior knowledge of Time Series Forecasting in Prosight/Data Science.
+ Knowledge of UOP Technologies.
+ Derive problem statement from ambiguous data, create a hypothesis, use analytics and tools to test hypothesis and form conclusions
+ Excellent technical expertise in all the areas of Descriptive, Predictive, and Prescriptive Analytics, including Optimization Analytics, Simulation & Advanced Machine Learning Algorithms.
+ Experience in cleaning, process, manipulate, and analyze data.
+ Ability to build scalable, user-centric applications -Building Models Data Science
+ Analysis of large amounts of historical data, determining suitability for modeling, data clean-up and filtering, pattern identification and variable creation, applying automated predictive analytics.
+ The focus is to support product, system, and solution through designing and developing pipelines.
+ Establishing additional work processes & documentation for the GSC.
+ Work with team to remove gaps in current solutions/tools to guide future development efforts with ProSight (UOP Internal platform) & content of solutions.
+ Work with the team to innovate - next-generation BIG DATA monitoring tools (Analytics using exception-based /Artificial Intelligence/Machine Learning) and work on operation dashboard for the GSC's sustainability & efficient operation.
+ Align with the Intention of the LST Business and ensure collective commitment for the GSC's Key results.
+ Part of 24x7 Operation of GSCCC Digital Insight
+ Working in 24x7 Shift is an integral part of this role. Work with GSCCC Center leader closely to make GSC as "Center of Excellence"
**Basic Candidate Qualification:**
- Bachelor's degree in chemical engineering
- Min of 12 years of experience in technical service or process operation/engineering/monitoring role within the refining and petrochemical industry.
**Additional Candidate Qualifications:**
+ Passion for visualizing hidden relationships in technical data with ProSight
+ Must demonstrate leadership to respond to customers seeking an urgent resolution to sometimes ambiguous technical needs quickly gain the Customer's trust and show accountability for problem resolution.
+ Excellent verbal, written, interpersonal communication & effective presentation skills
+ English language (oral and written)
+ Ability to multi-task
+ Be flexible to come in shift as a replacement in short notice
+ Exposure to techniques like forecasting, predictive methods, classification techniques, and segmentation is highly desirable.
+ Effective project management, presentation, and communication skills
+ Continuous learning and research-oriented mindset. Ability to think out of the box: Ability to come up with bright ideas and always looking at the next big thing in technology.
+ Have strong analytical skills; be able to interpret data, identify trends, and make suggestions for improvements
+ Knowledge of DataScience Open Source is added plus.
+ Proficiency in computer applications with emphasis on Data Analytics & Data Science is desirable
+ Creative approach to process development and customer-centric behavior
+ Comprehensive analytical, troubleshooting & problems solving skills.
+ Ability to work independently and in a team environment, focusing strongly on delivering SMART data results and identifying alternative solutions when challenges arise from unstructured data.
+ Ability to define the problem with limited information
+ This role may require global customer-facing and internal/external travel, up to 10% of the time.
Honeywell helps organizations solve the world's most complex challenges in automation, the future of aviation and energy transition. As a trusted partner, we provide actionable solutions and innovation through our Aerospace Technologies, Building Automation, Energy and Sustainability Solutions, and Industrial Automation business segments - powered by our Honeywell Forge software - that help make the world smarter, safer and more sustainable.
Honeywell is an equal opportunity employer. Qualified applicants will be considered without regard to age, race, creed, color, national origin, ancestry, marital status, affectional or sexual orientation, gender identity or expression, disability, nationality, sex, religion, or veteran status.
Be The First To Know
About the latest Chemical engineering Jobs in India !
Chemical Engr II
Posted 8 days ago
Job Viewed
Job Description
You will be an integrated network of technical professionals working together to provide outstanding technical insights. Customer Value is the GSC's key result to ensure we generate relevant insights from the extracted data for improved outcomes.
+ Be agile, innovating, and customer focused.
+ Review operations with customers and assisting with defining and quantifying customer benefits
+ Monitoring different UOP technologies process and identifying areas for improvement/optimization and assets requiring enhanced focus.
+ Provide readily available technical solutions/ work to get the solution to our customers.
+ Initial triage of technical issues with the escalation process to TS.
+ Proactively communicate insights from trends, establish patterns, diagnostic investigations, and solutions to prevent future issues.
+ Ensure upkeep of all solutions by troubleshooting the PM/PTA/PRA/POA/Benchmarking /Future Solutions on time to ensure high on-screen availability of the running solutions
+ Apply data mining to handle unstructured data to derive technical insights.
+ Perform descriptive and inferential statistics to summarize datasets.
+ Derive problem statement from ambiguous data, create a hypothesis, use analytics technology and tools to test hypothesis and form conclusions
+ Analysis of large amounts of historical data, determining suitability for modeling, data clean-up and filtering, pattern identification and variable creation, applying automated predictive analytics.
+ The focus is to support product, system, and solution through designing and developing pipelines.
+ Work with the team to innovate - next-generation BIG DATA monitoring tools (Analytics using exception-based /Artificial Intelligence/Machine Learning) and build an operation dashboard for the GSC's sustainability & efficient operation.
+ Align with the Intention of the LST Business and ensure collective commitment for the GSC's Key results.
+ Part of 24* 7 Operation of GSCCC Digital Insight
+ Working in 24*7 Shift is an integral part of this role. Work with GSCCC Operation leader closely to make GSC as Center of Excellence
**Basic Candidate Qualification:**
- BS degree in Chemical Engineering
**Additional Candidate Qualifications:**
+ Passion for visualizing hidden relationships in technical data with ProSight
+ Excellent verbal, written, interpersonal communication & effective presentation skills
+ English language (oral and written)
+ Ability to multi-task
+ Be flexible to come in shift as a replacement in short notice
+ Effective presentation, and communication skills
+ Continuous learning and research-oriented mindset. Ability to think out of the box: Ability to come up with bright ideas and always looking at the next big thing in technology.
+ Have strong analytical skills; be able to interpret data, identify trends, and make suggestions for improvements
+ Knowledge of DataScience Open Source is added plus.
+ Proficiency in computer applications with emphasis on Data Analytics & Data Science is desirable
+ Creative approach to process development and customer-centric behavior
+ Comprehensive analytical, troubleshooting & problems solving skills.
+ Ability to work independently and in a team environment, focusing strongly on delivering SMART data results and identifying alternative solutions when challenges arise from unstructured data.
+ Ability to define the problem with limited information
+ This role may require global customer-facing and internal/external travel, up to 10% of the time.
Honeywell helps organizations solve the world's most complex challenges in automation, the future of aviation and energy transition. As a trusted partner, we provide actionable solutions and innovation through our Aerospace Technologies, Building Automation, Energy and Sustainability Solutions, and Industrial Automation business segments - powered by our Honeywell Forge software - that help make the world smarter, safer and more sustainable.
Honeywell is an equal opportunity employer. Qualified applicants will be considered without regard to age, race, creed, color, national origin, ancestry, marital status, affectional or sexual orientation, gender identity or expression, disability, nationality, sex, religion, or veteran status.
Senior Consultant - Process Safety

Posted 10 days ago
Job Viewed
Job Description
- Supporting team members with process safety risk assessments and studies such as HAZIDs/HAZOPs, QRAs, ALARP demonstrations, COMAH/Offshore Safety Cases & Reports
- Working with your colleagues within the Health & Safety team, and the wider business, to establish and deliver marketing and proposal opportunities.
- Preparing and submitting thought leadership pieces and blogs to advance our presence in the market.
- Identifying new areas of potential work and engagement, to help evolve and expand our capabilities and experience.
The role can be offered at different levels depending on candidate's experience.
You'll be majorly work with a team of fifteen process safety professionals at various stages of their careers, from recent graduates through to industry experts. And, you will be part of team at India which is more than 100 members strong and working in different aspects of Earth & Environment.
- Recent projects we have completed have included:
o Process Safety studies for a capacity upgrade to the largest LNG storage and import terminal facility in Europe.
o Revalidation HAZOPs for multiple offshore oil and gas installations
o Guidance to an offshore oil and gas operator on ALARP standards for reinstatement of process plant
o Guidance on refreshing an offshore oil and gas operator's process safety auditing framework and protocols.
o An expert Process Safety audit of an upper tier COMAH site. S law.
Experience of applying your process safety knowledge within the oil and gas, chemical, nuclear or other high hazard sectors. This could perhaps be within an operating company, as a regulator, project engineer or consultant. - Operational experience of process safety management, including topics such as leadership, culture, competency, asset integrity, permit to work, isolations, and operating procedures. Experience of PSM auditing would be particularly welcome. - Knowledge of applicable UK H& S law.
Process Engineer- Water Projects
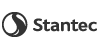
Posted 10 days ago
Job Viewed
Job Description
Globally, STANTEC sets the gold standard for the wet infrastructure sector as well as being the Number One engineering consultancy in the NCE listings. In the UK, STANTEC continues to be selected by Key Clients as one of their strategic consultancy providers. Therefore, we are now looking for the right people to join our team to help deliver these exciting opportunities.
This is a chance to join the Process Design Team providing support to the UK Region as well as across the globe in the delivery innovative project solutions.
The role will support STANTEC Project Technical Leads by providing technical expertise to ensure that projects are delivered to cost, schedule, technical and quality standards to meet both client and STANTEC expectations.
**Primary Purpose of Job:**
- Technical expertise in process engineering - flows and load analysis, treatment unit capacity assessment, knowledge of control philosophy, process block diagrams, awareness of P&IDs, and process unit sizing calculations
- Work as part of a team being involved in a variety of projects to help the development of solutions to delivery improvements and enhancements to process systems
- Prepare reports, calculations, drawings required to support the successful delivery of projects
- Maintain communication and develop on going contacts with clients as required
- Complete all work in line with STANTEC Core Values and in accordance with STANTEC Quality Systems and Project Quality Procedures
**Person Specifications:**
- Degree qualified (or equivalent) in Chemical, Civil or Process Engineering or other relevant subject.
- Professionally qualified BE - Chemical, Civil or Process Engineering and
- 10 to 15 years' relevant experience (water industry particularly with compliance issues and treatment plant operation with ideally knowledge of water and wastewater treatment processes) after graduate education.
- Baseline skills related to client service management, ie: should able to communicate and interface with counterparts, technical leaders, project managers in UK and other global regions; to build and maintain lasting, positive relationships.
- Baseline skills related to project management, ie: should be able to assist in scope definition; estimate level of effort; schedule; proactively communicate with team members in Pune office, as well as regional counterparts; coordinate across engineering disciplines.
- Experienced level of baseline skills, ie: professional and confident with the essential, basic business and communication skills that are required for career growth in all positions.
- Travel & other job demands
**Primary Location:** India | Pune
**Organization:** Stantec IN Business Unit
**Employee Status:** Regular
**Travel:** No
**Schedule:** Full time
**Job Posting:** 09/05/2025 08:05:45
**Req ID:** 1000602