24 Maintenance Planning jobs in India
Core Maintenance Planning Lead
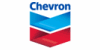
Posted 7 days ago
Job Viewed
Job Description
2
**About the position:**
The Core Maintenance Planning Lead is a team member of the Maintenance and Turnaround organization within the Chevron ENGINE Center and provides Maintenance Planning support to Chevron's Refining and Liquified Natural Gas (LNG) assets. The Core Maintenance Planning Lead oversees a team of maintenance planners and schedulers that are responsible for developing detailed plans and schedules to execute planned maintenance (both preventative (PM) and corrective (CM)) and project work. Responsibilities will include integrating Routine Maintenance planning/scheduling activities with Operations, Maintenance, and Technical; and integrating capital project planning/scheduling activities.
**Key responsibilities:**
+ Coordinates the planning and scheduling of all non-turnaround field maintenance work at the site that is performed by various crafts.
+ Provide SME support on planning, estimating, and scheduling for Chevron executed project work.
+ Ensures the development of work packages of consistent high quality in compliance with Chevron standards.
+ Drive accountability regarding the use of standard planning and estimating tools and practices. Accountable for the growth and development of planners and schedulers.
+ Delivering quality execution work plans and updates on scope status and forecast. Collaborate with site representatives to determine work scope to be executed by maintenance teams.
+ Works closely with Operations to ensure schedules are effectively integrated into the operating plan.
+ Accountable to partner with the Asset Maintenance Team Leads in all crafts to feed planned work into the asset integrated plan/workflow and prepare the work for the field.
+ Develop tools to streamline cost and execution forecasting accuracy and report on status at individual project and portfolio level. Seek opportunities to improve planning and scheduling accuracy as well as to remove inefficiencies from planning and scheduling activities
+ Work with Construction Services team to integrate Chevron executed scope into a master project schedule
+ Clearly communicate scope progress to customers, stakeholders, and team members. Assist in growing Routine/Planned Maintenance work process competency within the ENGINE
+ Ensures Lessons Learned reviews are completed for each FEL event and drive subsequent improvement initiatives.
+ Proactively supports backlog management.
+ Responsible for developing and improving maintenance resource forecasting for the development Asset's 5-year Work Plan and Budget.
+ Participate in hiring and organizational design as required.
+ Support succession planning discussions with leadership teams for the ENGINE maintenance and turnaround organization.
**Required Qualifications:**
+ Degree in relevant Engineering or Maintenance Discipline
+ Previous Oil and Gas experience in a Maintenance Planning Leadership Position.
+ Strong technical background in planning and scheduling tools - JDE, SAP, Prometheus, Primavera P6.
+ Understanding of planning processes including constructability, advanced work packaging, work planning (schedule, resources, cost), project scoping, contract planning and management, progress measurement/controls, and materials management.
+ Knowledgeable in core maintenance and technical project planning and scheduling industry best practices. Experience with mechanical, electrical, instrumentation/controls, fabrication, inspection and related disciplines while also having a good working knowledge of complex facility operations, preferably LNG facilities.
+ Strong leadership skills and experience in managing site staff.
+ Demonstrated knowledge of supply chain logistics to ensure all work can be completed in remote locations.
+ Demonstrated skills in time management to drive effective communications between staff and the maintainable assets
**Preferred Qualifications:**
+ 10+ years relevant turnaround execution experience providing technical and maintenance planning support to plant maintenance teams in a complex oil and gas operating environment, preferred.
+ Familiarity in supporting Operations within the Refining or LNG industry is desirable.
+ Experience in mentoring, coaching, and training is desirable.
Chevron ENGINE supports global operations, supporting business requirements across the world. Accordingly, the work hours for employees will be aligned to support business requirements. The standard work week will be Monday to Friday. Working hours are 8:00am to 5:00pm or 1.30pm to 10.30pm.
Chevron participates in E-Verify in certain locations as required by law.
Chevron Corporation is one of the world's leading integrated energy companies. Through its subsidiaries that conduct business worldwide, the company is involved in virtually every facet of the energy industry. Chevron explores for, produces and transports crude oil and natural gas; refines, markets and distributes transportation fuels and lubricants; manufactures and sells petrochemicals and additives; generates power; and develops and deploys technologies that enhance business value in every aspect of the company's operations. Chevron is based in Houston, Texas. More information about Chevron is available at .
Chevron is an Equal Opportunity / Affirmative Action employer. Qualified applicants will receive consideration for employment without regard to race, color, religion, sex, sexual orientation, gender identity, national origin, disability or protected veteran status, or other status protected by law or regulation.
Core Maintenance Planning Team Lead
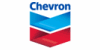
Posted 7 days ago
Job Viewed
Job Description
1
**About the position:**
The Core Maintenance Planning Team Lead is a part of the Maintenance and Turnaround organization within the Chevron ENGINE Center and provides routine maintenance planning support to Chevron's Refining and Liquified Natural Gas (LNG) assets. The Core Maintenance Planning Team Lead oversees a team of maintenance planners, schedulers, and permit writers who are responsible for developing detailed plans and schedules to execute planned maintenance (both preventative (PM) and corrective (CM)) and project work. Responsibilities will include integrating Routine Maintenance planning/scheduling activities with Operations, Maintenance, and Technical; and integrating capital project planning/scheduling activities. The Core Maintenance Team Lead interfaces collaboratively with multiple disciplines including Operations, Technical, Routine Maintenance, site inspections etc.
**Key responsibilities:**
+ Coordinates the planning and scheduling of all non-turnaround routine maintenance work at the site that is performed by various crafts.
+ Provide SME support on planning, estimating, and scheduling for Chevron executed project work.
+ Ensures the development of work packages of consistent high quality in compliance with Chevron standards.
+ Drive accountability regarding the use of standard planning and estimating tools and practices. Accountable for the growth and development of planners and schedulers.
+ Delivering quality execution work plans and updates on scope status and forecast. Collaborate with site representatives to determine work scope to be executed by maintenance teams.
+ Works closely with Operations to ensure schedules are effectively integrated into the operating plan.
+ Accountable to partner with the Asset Maintenance Team Leads in all crafts to feed planned work into the asset integrated plan/workflow and prepare the work for the field.
+ Develop tools to streamline cost and execution forecasting accuracy and report on status at individual project and portfolio level. Seek opportunities to improve planning and scheduling accuracy as well as to remove inefficiencies from planning and scheduling activities
+ Work with Construction Services team to integrate Chevron executed scope into a master project schedule
+ Clearly communicate scope progress to customers, stakeholders, and team members. Assist in growing Routine/Planned Maintenance work process competency within the ENGINE
+ Ensures Lessons Learned reviews are completed for each FEL event and drive subsequent improvement initiatives.
+ Proactively supports backlog management.
+ Responsible for developing and improving maintenance resource forecasting for the development Asset's 5-year Work Plan and Budget.
+ Participate in hiring and organizational design as required.
+ Support succession planning discussions with leadership teams for the ENGINE maintenance and turnaround organization.
**Required Qualifications:**
+ Degree in relevant Engineering or Maintenance Discipline
+ Previous Oil and Gas experience in a Maintenance Planning Leadership Position.
+ Strong technical background in planning and scheduling tools - JDE, SAP, Prometheus, Primavera P6.
+ Understanding of planning processes including constructability, advanced work packaging, work planning (schedule, resources, cost), project scoping, contract planning and management, progress measurement/controls, and materials management.
+ Knowledgeable in core maintenance and technical project planning and scheduling industry best practices. Experience with mechanical, electrical, instrumentation/controls, fabrication, inspection and related disciplines while also having a good working knowledge of complex facility operations, preferably LNG facilities.
+ Strong leadership skills and experience in managing site staff.
+ Demonstrated knowledge of supply chain logistics to ensure all work can be completed in remote locations.
+ Demonstrated skills in time management to drive effective communications between staff and the maintainable assets
**Preferred Qualifications:**
+ 15+ years in relevant maintenance planning and execution experience providing technical and maintenance planning support to plant maintenance teams in a complex oil and gas operating environment, preferred.
+ Familiarity in supporting Operations within the Refining or LNG industry is desirable.
+ Demonstrated leadership or supervisory experience is highly regarded.
Chevron ENGINE supports global operations, supporting business requirements across the world. Accordingly, the work hours for employees will be aligned to support business requirements. The standard work week will be Monday to Friday. Working hours are 8:00am to 5:00pm or 1.30pm to 10.30pm.
Chevron participates in E-Verify in certain locations as required by law.
Chevron Corporation is one of the world's leading integrated energy companies. Through its subsidiaries that conduct business worldwide, the company is involved in virtually every facet of the energy industry. Chevron explores for, produces and transports crude oil and natural gas; refines, markets and distributes transportation fuels and lubricants; manufactures and sells petrochemicals and additives; generates power; and develops and deploys technologies that enhance business value in every aspect of the company's operations. Chevron is based in Houston, Texas. More information about Chevron is available at .
Chevron is an Equal Opportunity / Affirmative Action employer. Qualified applicants will receive consideration for employment without regard to race, color, religion, sex, sexual orientation, gender identity, national origin, disability or protected veteran status, or other status protected by law or regulation.
Manager - Engine Maintenance Planning & Analytics
Posted 8 days ago
Job Viewed
Job Description
Come join us to create what's next. Let's define tomorrow, together.
**Description**
At United, we have some of the best aircraft in the world. Our Technical Operations team is full of aircraft maintenance technicians, engineers, planners, ground equipment and facilities professionals, and supply chain teams that help make sure they're well taken care of and ready to get our customers to their desired destinations. If you're ready to work on our planes, join our Tech Ops experts and help keep our fleet in tip-top shape.
**Job overview and responsibilities**
The Manager (Mgr) - Engine Maintenance (Mx) Planning & Analytics leads a team responsible for data-driven engine maintenance planning and material forecasting. This role oversees the development of analytical tools, dashboards, and forecasting models to support strategic decision-making for all engine and APU programs. In addition, to driving data analytics, the Mgr collaborates with Global Procurement, Inventory Planning, and Finance to optimize material planning and ensure the timely availability of critical engine components. The Mgr is also responsible for continuously improving forecasting accuracy and operational efficiency to support long-term maintenance planning.
+ Design, create, manage dashboards regarding engine removals, spare engine availability, shop turn time, engine strip time, engine build time, and other related information
+ Lead the methodology of an engine parts forecast model for short-term (6 to 18 months) and long-term (> 18 months) use cases that is applicable to multiple fleets and difference specifications
+ Lead project management of the engine procurement cycle by reporting on current and future engine part inventory
+ Manage direct reports and provide professional development to the team
+ Create and deliver engine maintenance reports that will be presented to leadership
+ Perform ad-hoc data analysis and modeling of engine programs to support end users such as Network planning, Fleet, Global Procurement, Finance, and EMM
+ Develop and coordinate solutions to automate, collect/store, and audit data for accuracy
**This position is offered on local terms and conditions. Expatriate assignments and sponsorship for employment visas, even on a time-limited visa status, will not be awarded. This position is for**
**United Airlines Business Services Pvt. Ltd - a wholly owned subsidiary of United Airlines Inc.**
**Qualifications**
**What's needed to succeed (Minimum Qualifications):**
+ Bachelor's degree in Engineering, Supply Chain, Business, Science, Mathematics, Finance, Statistics
+ 3+ years' experience in the aviation and/or aerospace industry
+ 2+ years' of experience in an analytics and/or quantitative role with demonstrated experience building and maintaining complex analytical models
+ 6+ years' of engineering / business / supply chain work experience
+ Ability to review data, formulate a model, draw conclusions, and use data-based analysis to inform others
+ Demonstrated ability to lead a team
+ Strong organizational and continuous improvement skills
+ Demonstrated ability to understand technical information
+ Ability to effectively communicate both verbally and in-writing to technical and non-technical audiences
+ Ability to manage complex workload to effectively accomplish assignments with limited supervision
+ Skilled in computer programming languages such as (but not limited to) Python, Ppyspark, Jjava Sscript, HTML, SQL, R, and/or VBA
+ Must be legally authorized to work in India for any employer without sponsorship
+ Must be fluent in English (written and spoken)
+ Successful completion of interview required to meet job qualification
+ Reliable, punctual attendance is an essential function of the position
**What will help you propel from the pack (Preferred Qualifications):**
+ Master's degree
+ MBA, MS Engineering, MS Data Analytics
+ Project management experience by leading teams through indirect influence
+ Experience managing a team
+ Experience using statistical analysis tools for forecasting parts or events
+ Process improvement experience
+ 3+ years' experience in aircraft or engine maintenance management
+ Strong aviation and/or engine business acumen
+ Detailed understanding of jet engine components
+ Knowledge of engine maintenance planning/overhaul events
+ Proficiency in Palantir/Foundry
+ Analytics using structured and unstructured data, including statistical inference, parametric and non-parametric predictive models, machine learning, natural language processing
Manager - Engine Maintenance Planning & Analytics
Posted today
Job Viewed
Job Description
Qualifications What’s needed to succeed (Minimum Qualifications):At United, we have some of the best aircraft in the world. Our Technical Operations team is full of aircraft maintenance technicians, engineers, planners, ground equipment and facilities professionals, and supply chain teams that help make sure they’re well taken care of and ready to get our customers to their desired destinations. If you’re ready to work on our planes, join our Tech Ops experts and help keep our fleet in tip-top shape.
Job overview and responsibilities
The Manager (Mgr) – Engine Maintenance (Mx) Planning & Analytics leads a team responsible for data-driven engine maintenance planning and material forecasting. This role oversees the development of analytical tools, dashboards, and forecasting models to support strategic decision-making for all engine and APU programs. In addition, to driving data analytics, the Mgr collaborates with Global Procurement, Inventory Planning, and Finance to optimize material planning and ensure the timely availability of critical engine components. The Mgr is also responsible for continuously improving forecasting accuracy and operational efficiency to support long-term maintenance planning.
- Design, create, manage dashboards regarding engine removals, spare engine availability, shop turn time, engine strip time, engine build time, and other related information
- Lead the methodology of an engine parts forecast model for short-term (6 to 18 months) and long-term (> 18 months) use cases that is applicable to multiple fleets and difference specifications
- Lead project management of the engine procurement cycle by reporting on current and future engine part inventory
- Manage direct reports and provide professional development to the team
- Create and deliver engine maintenance reports that will be presented to leadership
- Perform ad-hoc data analysis and modeling of engine programs to support end users such as Network planning, Fleet, Global Procurement, Finance, and EMM
- Develop and coordinate solutions to automate, collect/store, and audit data for accuracy
This position is offered on local terms and conditions. Expatriate assignments and sponsorship for employment visas, even on a time-limited visa status, will not be awarded. This position is for
United Airlines Business Services Pvt. Ltd - a wholly owned subsidiary of United Airlines Inc.
- Bachelor's degree in Engineering, Supply Chain, Business, Science, Mathematics, Finance, Statistics
- 3+ years’ experience in the aviation and/or aerospace industry
- 2+ years’ of experience in an analytics and/or quantitative role with demonstrated experience building and maintaining complex analytical models
- 6+ years’ of engineering / business / supply chain work experience
- Ability to review data, formulate a model, draw conclusions, and use data-based analysis to inform others
- Demonstrated ability to lead a team
- Strong organizational and continuous improvement skills
- Demonstrated ability to understand technical information
- Ability to effectively communicate both verbally and in-writing to technical and non-technical audiences
- Ability to manage complex workload to effectively accomplish assignments with limited supervision
- Skilled in computer programming languages such as (but not limited to) Python, Ppyspark, Jjava Sscript, HTML, SQL, R, and/or VBA
- Must be legally authorized to work in India for any employer without sponsorship
- Must be fluent in English (written and spoken)
- Successful completion of interview required to meet job qualification
- Reliable, punctual attendance is an essential function of the position
- Master's degree
- MBA, MS Engineering, MS Data Analytics
- Project management experience by leading teams through indirect influence
- Experience managing a team
- Experience using statistical analysis tools for forecasting parts or events
- Process improvement experience
- 3+ years’ experience in aircraft or engine maintenance management
- Strong aviation and/or engine business acumen
- Detailed understanding of jet engine components
- Knowledge of engine maintenance planning/overhaul events
- Proficiency in Palantir/Foundry
- Analytics using structured and unstructured data, including statistical inference, parametric and non-parametric predictive models, machine learning, natural language processing
Senior Analyst - Engine Maintenance Planning & Analytics
Posted 8 days ago
Job Viewed
Job Description
Come join us to create what's next. Let's define tomorrow, together.
**Description**
At United, we have some of the best aircraft in the world. Our Technical Operations team is full of aircraft maintenance technicians, engineers, planners, ground equipment and facilities professionals, and supply chain teams that help make sure they're well taken care of and ready to get our customers to their desired destinations. If you're ready to work on our planes, join our Tech Ops experts and help keep our fleet in tip-top shape.
**Job overview and responsibilities**
The Sr. Analyst - Engine Maintenance (Mx) Planning conducts data analysis and program modeling for all engine and APU types, supporting strategic decision-making across TechOps. This role develops forecast models, builds dashboards, and creates business tools to enhance operational efficiency and long-term maintenance planning. In collaboration with the Engine Mx Management (EMM) team, San Francisco Engine Mx Center, and other stakeholders, the Sr. Analyst ensures data accuracy by validating sources and refining methodologies. Additional responsibilities may include partnering with Inventory Planning and Global Procurement to optimize engine parts inventory and procurement strategies.
+ Develop, implement, and maintain agile long-term engine/APU forecasts
+ Provide project management by tracking, analyzing, and reporting on current and/or future engine/APU part inventory
+ Performs ad-hoc data analysis and modeling of engine programs to support end users across the organization
+ Identify opportunities to automate data collection, monitoring, and other workflows, and create necessary solutions
+ Audit and review data for accuracy and implement corrections as appropriate
+ Prepare reports for stakeholder updates
**This position is offered on local terms and conditions. Expatriate assignments and sponsorship for employment visas, even on a time-limited visa status, will not be awarded.**
**Qualifications**
**What's needed to succeed (Minimum Qualifications):**
+ Bachelor's degree in Engineering, Supply Chain, Business, Science, Mathematics, Statistics, or Finance
+ 4+ years' experience in data analysis, project experience
+ Experience building forecasts and doing analysis
+ Proficiency in performing complex analyses or models
+ Skilled in computer programming languages and database systems such as (but not limited to) Python, pyspark, Java Script, SQL, HTML, R, and/or VBA
+ Ability to effectively communicate both verbally and in writing, tailoring delivery to technical and non-technical audiences
+ Strong organizational and continuous improvement skills
+ Ability to manage complex workload to effectively accomplish assignments and projects with limited supervision
+ Proficiency in Microsoft Office Suite including Word, PowerPoint, and Excel
+ Effectively manage projects with multiple stakeholders
+ Must be legally authorized to work in India for any employer without sponsorship
+ Must be fluent in English and Hindi (written and spoken)
+ Successful completion of interview required to meet job qualification
+ Reliable, punctual attendance is an essential function of the position
**What will help you propel from the pack (Preferred Qualifications):**
+ Master's degree
+ MBA, MS Engineering, MS Data Analytics
+ Experience in aircraft engine maintenance
+ Process improvement experience
+ Experience using statistical analysis tools for forecasting
+ Strong aviation business acumen
+ Detailed understanding of jet engine maintenance and components
+ Proficiency in Palantir/Foundry
+ Analytics using structured and unstructured data, including statistical inference, parametric and non-parametric predictive models, machine learning, natural language processing
Senior Analyst - Engine Maintenance Planning & Analytics
Posted today
Job Viewed
Job Description
Qualifications What’s needed to succeed (Minimum Qualifications):At United, we have some of the best aircraft in the world. Our Technical Operations team is full of aircraft maintenance technicians, engineers, planners, ground equipment and facilities professionals, and supply chain teams that help make sure they’re well taken care of and ready to get our customers to their desired destinations. If you’re ready to work on our planes, join our Tech Ops experts and help keep our fleet in tip-top shape.
Job overview and responsibilities
The Sr. Analyst – Engine Maintenance (Mx) Planning conducts data analysis and program modeling for all engine and APU types, supporting strategic decision-making across TechOps. This role develops forecast models, builds dashboards, and creates business tools to enhance operational efficiency and long-term maintenance planning. In collaboration with the Engine Mx Management (EMM) team, San Francisco Engine Mx Center, and other stakeholders, the Sr. Analyst ensures data accuracy by validating sources and refining methodologies. Additional responsibilities may include partnering with Inventory Planning and Global Procurement to optimize engine parts inventory and procurement strategies.
- Develop, implement, and maintain agile long-term engine/APU forecasts
- Provide project management by tracking, analyzing, and reporting on current and/or future engine/APU part inventory
- Performs ad-hoc data analysis and modeling of engine programs to support end users across the organization
- Identify opportunities to automate data collection, monitoring, and other workflows, and create necessary solutions
- Audit and review data for accuracy and implement corrections as appropriate
- Prepare reports for stakeholder updates
This position is offered on local terms and conditions. Expatriate assignments and sponsorship for employment visas, even on a time-limited visa status, will not be awarded.
- Bachelor's degree in Engineering, Supply Chain, Business, Science, Mathematics, Statistics, or Finance
- 4+ years’ experience in data analysis, project experience
- Experience building forecasts and doing analysis
- Proficiency in performing complex analyses or models
- Skilled in computer programming languages and database systems such as (but not limited to) Python, pyspark, Java Script, SQL, HTML, R, and/or VBA
- Ability to effectively communicate both verbally and in writing, tailoring delivery to technical and non-technical audiences
- Strong organizational and continuous improvement skills
- Ability to manage complex workload to effectively accomplish assignments and projects with limited supervision
- Proficiency in Microsoft Office Suite including Word, PowerPoint, and Excel
- Effectively manage projects with multiple stakeholders
- Must be legally authorized to work in India for any employer without sponsorship
- Must be fluent in English and Hindi (written and spoken)
- Successful completion of interview required to meet job qualification
- Reliable, punctual attendance is an essential function of the position
- Master's degree
- MBA, MS Engineering, MS Data Analytics
- Experience in aircraft engine maintenance
- Process improvement experience
- Experience using statistical analysis tools for forecasting
- Strong aviation business acumen
- Detailed understanding of jet engine maintenance and components
- Proficiency in Palantir/Foundry
- Analytics using structured and unstructured data, including statistical inference, parametric and non-parametric predictive models, machine learning, natural language processing
Core Maintenance Planning Lead Bengaluru, India
Posted today
Job Viewed
Job Description
About the position:
The Core Maintenance Planning Lead is a team member of the Maintenance and Turnaround organization within the Chevron ENGINE Center and provides Maintenance Planning support to Chevron's Refining and Liquified Natural Gas (LNG) assets. The Core Maintenance Planning Lead oversees a team of maintenance planners and schedulers that are responsible for developing detailed plans and schedules to execute planned maintenance (both preventative (PM) and corrective (CM)) and project work. Responsibilities will include integrating Routine Maintenance planning/scheduling activities with Operations, Maintenance, and Technical; and integrating capital project planning/scheduling activities.
Key responsibilities:
Coordinates the planning and scheduling of all non-turnaround field maintenance work at the site that is performed by various crafts.
Provide SME support on planning, estimating, and scheduling for Chevron executed project work.
Ensures the development of work packages of consistent high quality in compliance with Chevron standards.
Drive accountability regarding the use of standard planning and estimating tools and practices. Accountable for the growth and development of planners and schedulers.
Delivering quality execution work plans and updates on scope status and forecast. Collaborate with site representatives to determine work scope to be executed by maintenance teams.
Works closely with Operations to ensure schedules are effectively integrated into the operating plan.
Accountable to partner with the Asset Maintenance Team Leads in all crafts to feed planned work into the asset integrated plan/workflow and prepare the work for the field.
Develop tools to streamline cost and execution forecasting accuracy and report on status at individual project and portfolio level. Seek opportunities to improve planning and scheduling accuracy as well as to remove inefficiencies from planning and scheduling activities
Work with Construction Services team to integrate Chevron executed scope into a master project schedule
Clearly communicate scope progress to customers, stakeholders, and team members. Assist in growing Routine/Planned Maintenance work process competency within the ENGINE
Ensures Lessons Learned reviews are completed for each FEL event and drive subsequent improvement initiatives.
Proactively supports backlog management.
Responsible for developing and improving maintenance resource forecasting for the development Asset’s 5-year Work Plan and Budget.
Participate in hiring and organizational design as required.
Support succession planning discussions with leadership teams for the ENGINE maintenance and turnaround organization.
Required Qualifications:
Degree in relevant Engineering or Maintenance Discipline
Previous Oil and Gas experience in a Maintenance Planning Leadership Position.
Strong technical background in planning and scheduling tools – JDE, SAP, Prometheus, Primavera P6.
Understanding of planning processes including constructability, advanced work packaging, work planning (schedule, resources, cost), project scoping, contract planning and management, progress measurement/controls, and materials management.
Knowledgeable in core maintenance and technical project planning and scheduling industry best practices. Experience with mechanical, electrical, instrumentation/controls, fabrication, inspection and related disciplines while also having a good working knowledge of complex facility operations, preferably LNG facilities.
Strong leadership skills and experience in managing site staff.
Demonstrated knowledge of supply chain logistics to ensure all work can be completed in remote locations.
Demonstrated skills in time management to drive effective communications between staff and the maintainable assets
Preferred Qualifications:
10+ years relevant turnaround execution experience providing technical and maintenance planning support to plant maintenance teams in a complex oil and gas operating environment, preferred.
Familiarity in supporting Operations within the Refining or LNG industry is desirable.
Experience in mentoring, coaching, and training is desirable.
Chevron ENGINE supports global operations, supporting business requirements across the world. Accordingly, the work hours for employees will be aligned to support business requirements. The standard work week will be Monday to Friday. Working hours are 8:00am to 5:00pm or 1.30pm to 10.30pm.
Chevron participates in E-Verify in certain locations as required by law.
Bengaluru, Karnataka
Privacy and Terms and Conditions
We respect the privacy of candidates for employment. This Privacy Notice sets forth how we will use the information we obtain when you apply for a position through this career site. If you do not consent to the terms of this Privacy Notice, please do not submit information to us.
Please access the Global Application Statements, select the country where you are applying for employment. By applying, you acknowledge that you have read and agree to the country specific statement.
Terms of Use
Be The First To Know
About the latest Maintenance planning Jobs in India !
Core Maintenance Planning Team Lead Bengaluru, India
Posted today
Job Viewed
Job Description
About the position:
The Core Maintenance Planning Team Lead is a part of the Maintenance and Turnaround organization within the Chevron ENGINE Center and provides routine maintenance planning support to Chevron's Refining and Liquified Natural Gas (LNG) assets. The Core Maintenance Planning Team Lead oversees a team of maintenance planners, schedulers, and permit writers who are responsible for developing detailed plans and schedules to execute planned maintenance (both preventative (PM) and corrective (CM)) and project work. Responsibilities will include integrating Routine Maintenance planning/scheduling activities with Operations, Maintenance, and Technical; and integrating capital project planning/scheduling activities. The Core Maintenance Team Lead interfaces collaboratively with multiple disciplines including Operations, Technical, Routine Maintenance, site inspections etc.
Key responsibilities:
Coordinates the planning and scheduling of all non-turnaround routine maintenance work at the site that is performed by various crafts.
Provide SME support on planning, estimating, and scheduling for Chevron executed project work.
Ensures the development of work packages of consistent high quality in compliance with Chevron standards.
Drive accountability regarding the use of standard planning and estimating tools and practices. Accountable for the growth and development of planners and schedulers.
Delivering quality execution work plans and updates on scope status and forecast. Collaborate with site representatives to determine work scope to be executed by maintenance teams.
Works closely with Operations to ensure schedules are effectively integrated into the operating plan.
Accountable to partner with the Asset Maintenance Team Leads in all crafts to feed planned work into the asset integrated plan/workflow and prepare the work for the field.
Develop tools to streamline cost and execution forecasting accuracy and report on status at individual project and portfolio level. Seek opportunities to improve planning and scheduling accuracy as well as to remove inefficiencies from planning and scheduling activities
Work with Construction Services team to integrate Chevron executed scope into a master project schedule
Clearly communicate scope progress to customers, stakeholders, and team members. Assist in growing Routine/Planned Maintenance work process competency within the ENGINE
Ensures Lessons Learned reviews are completed for each FEL event and drive subsequent improvement initiatives.
Proactively supports backlog management.
Responsible for developing and improving maintenance resource forecasting for the development Asset’s 5-year Work Plan and Budget.
Participate in hiring and organizational design as required.
Support succession planning discussions with leadership teams for the ENGINE maintenance and turnaround organization.
Required Qualifications:
Degree in relevant Engineering or Maintenance Discipline
Previous Oil and Gas experience in a Maintenance Planning Leadership Position.
Strong technical background in planning and scheduling tools – JDE, SAP, Prometheus, Primavera P6.
Understanding of planning processes including constructability, advanced work packaging, work planning (schedule, resources, cost), project scoping, contract planning and management, progress measurement/controls, and materials management.
Knowledgeable in core maintenance and technical project planning and scheduling industry best practices. Experience with mechanical, electrical, instrumentation/controls, fabrication, inspection and related disciplines while also having a good working knowledge of complex facility operations, preferably LNG facilities.
Strong leadership skills and experience in managing site staff.
Demonstrated knowledge of supply chain logistics to ensure all work can be completed in remote locations.
Demonstrated skills in time management to drive effective communications between staff and the maintainable assets
Preferred Qualifications:
15+ years in relevant maintenance planning and execution experience providing technical and maintenance planning support to plant maintenance teams in a complex oil and gas operating environment, preferred.
Familiarity in supporting Operations within the Refining or LNG industry is desirable.
Demonstrated leadership or supervisory experience is highly regarded.
Chevron ENGINE supports global operations, supporting business requirements across the world. Accordingly, the work hours for employees will be aligned to support business requirements. The standard work week will be Monday to Friday. Working hours are 8:00am to 5:00pm or 1.30pm to 10.30pm.
Chevron participates in E-Verify in certain locations as required by law.
Bengaluru, Karnataka
Privacy and Terms and Conditions
We respect the privacy of candidates for employment. This Privacy Notice sets forth how we will use the information we obtain when you apply for a position through this career site. If you do not consent to the terms of this Privacy Notice, please do not submit information to us.
Please access the Global Application Statements, select the country where you are applying for employment. By applying, you acknowledge that you have read and agree to the country specific statement.
Terms of Use
Facility & Maintenance Manager
Posted today
Job Viewed
Job Description
Job description
About the Role
The Facility & Maintenance Manager will be responsible for the smooth operation, maintenance, and safety of The Whole
Truth’s facilities and equipment. This includes overseeing daily maintenance operations, managing teams, implementing
preventative maintenance schedules, and ensuring compliance with safety standards.
Key Responsibilities
1. Facility Maintenance:
o Inspect facilities periodically to identify and address maintenance needs.
o Manage and maintain building systems, including heating, ventilation, and electrical systems.
o Ensure facilities remain safe, functional, and compliant with health regulations.
2. Team Management:
o Recruit, train, and supervise maintenance technicians.
o Assign and monitor weekly maintenance schedules.
o Hire and oversee tradesmen (electricians, plumbers, etc.) for specialized tasks.
3. Preventive Maintenance:
o Develop and implement preventive maintenance programs.
o Monitor equipment and systems to minimize downtime and extend lifespan.
o Maintain accurate records of inspections, repairs, and maintenance activities.
4. Inventory and Budget Management:
o Track inventory levels of materials and equipment.
o Contribute to the development and management of the maintenance budget.
5. Project Coordination:
o Coordinate renovations, installations, and facility improvement projects.
o Ensure projects are completed within deadlines and budgets.
6. Health & Safety:
o Conduct regular safety inspections and ensure compliance with safety regulations.
o Develop and implement emergency response plans.
Personality Attributes
Likeable and patient demeanor.
High attention to detail.
trong sense of ownership and accountability.
Required Skills
uick learner with strong logic and analytical abilities.
xcellent communication skills in Hindi, Marathi and English.
asic data analysis skills in Excel and Google Sheets.
Sr Officer-Facility Maintenance
Posted today
Job Viewed
Job Description
The Facility Management team provides value add by:
Proposing and implementing FM budgets, and monitors related spendings.
Ensuring all technical and legal regulations with regards to facility state and operations are met at all times.
A job at this level:
Executes recurring day-to-day administration or service-related operations, in processes as assigned.
Selects, apply and/or adapt procedures and practices to cover all occurring variances in work.
Serves internal stakeholder or clients with accurate and reliable execution of assigned processes.
Provides 1st level support in administrative subjects, for customers or for other stakeholders involved.
Maintains relations and exchanges information as appropriate to ensure smooth workflow between related work areas.